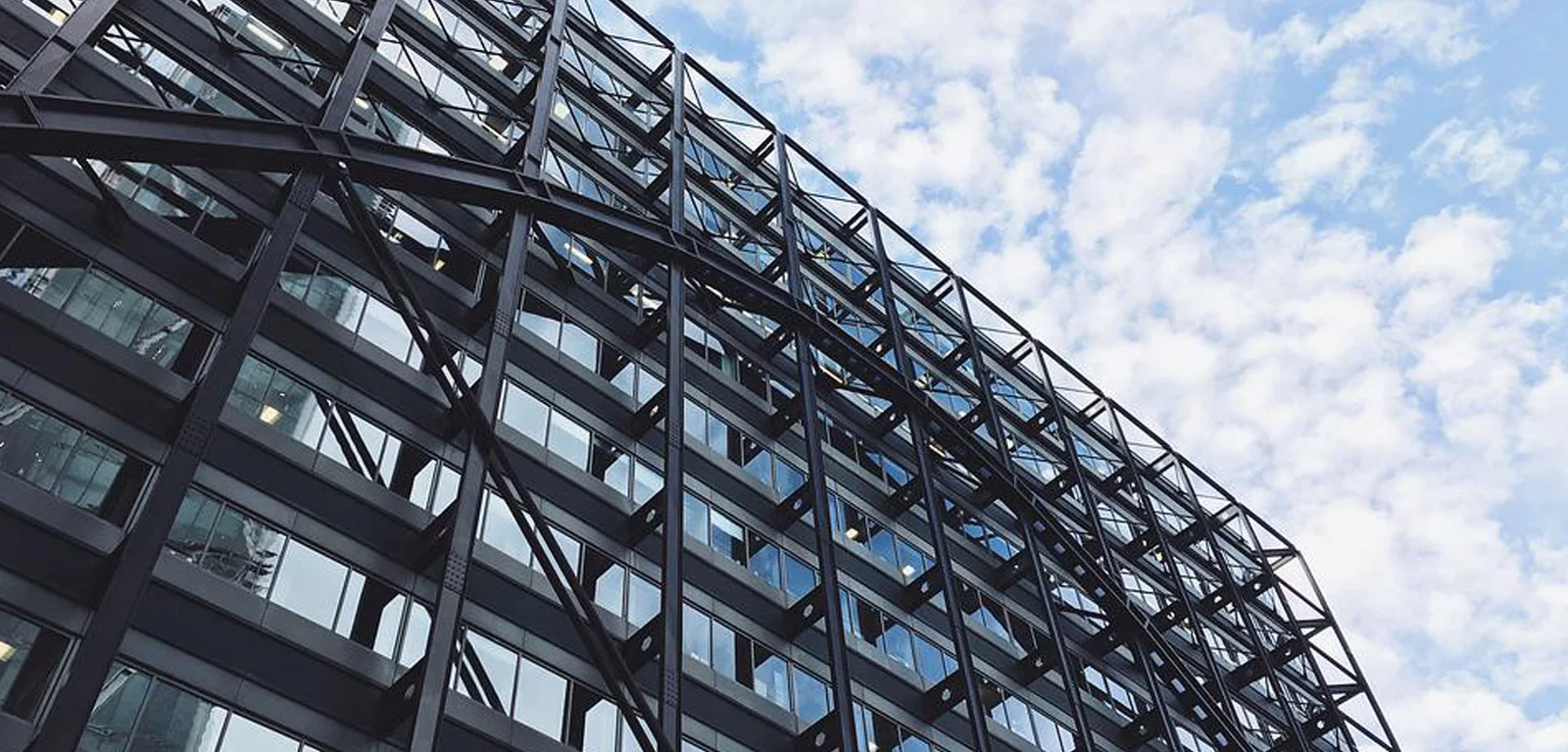
Why Pre-Engineered Buildings Are the Future of Construction in Nepal
Nepal’s construction landscape is evolving at a remarkable pace. With rapid urbanization, expanding industries, and a growing need for sustainable infrastructure, the demand for innovative building solutions has never been higher.
Enter pre-engineered buildings (PEBs)—a game-changing approach that’s redefining the future of construction in Nepal. But what makes pre-engineered buildings the future of Nepal’s infrastructure?
In this blog, we’ll dive into the benefits of PEBs, their applications, and why they’re poised to shape Nepal’s skyline for years to come.
What Are Pre-Engineered Buildings?
Pre-engineered buildings are structures designed and manufactured off-site using advanced engineering techniques. These components—think steel frameworks, wall panels, and roofing systems—are precision-crafted in factories, then shipped to the construction site for quick assembly.
Unlike traditional construction, which relies heavily on on-site labor and materials, PEBs streamline the process, making them ideal for a variety of projects, from industrial warehouses to commercial complexes and even residential homes.
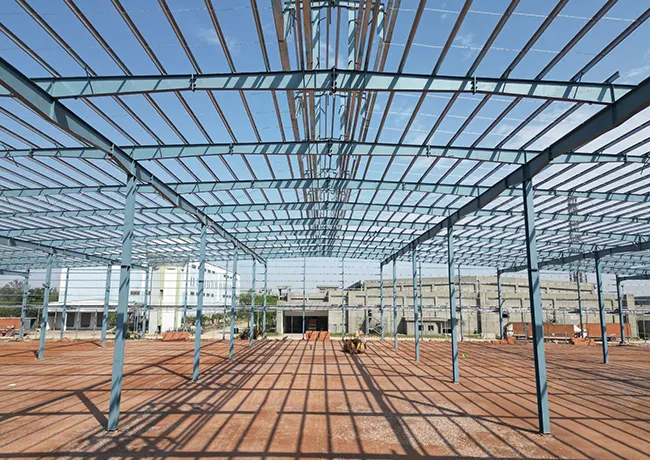
Why are pre-engineered buildings the future? Their efficiency, affordability, and adaptability make them a perfect fit for Nepal’s unique challenges, including rugged terrain, unpredictable weather, and seismic risks.
Why Pre-Engineered Buildings Are the Future in Nepal?
Nepal’s construction industry faces hurdles like limited resources, logistical bottlenecks, and a need for sustainable practices. Pre-engineered buildings address these challenges head-on. Let’s explore why they’re becoming the go-to choice for builders and businesses alike.
1. Lightning-Fast Construction Times
Time is money, especially in Nepal’s fast-growing economy. Traditional construction methods often drag on for months, delayed by monsoons, supply chain issues, or labor shortages.
Pre-engineered buildings flip the script. Since most components are pre-fabricated in controlled factory environments, on-site assembly is quick and efficient.
For example, a typical warehouse built with traditional methods might take six months to complete. A PEB warehouse? It could be up and running in half that time. This speed is a lifeline for businesses eager to launch operations or expand in Nepal’s competitive market.
2. Cost-Effectiveness That Hits the Sweet Spot
Budget constraints are a reality for many projects in Nepal, whether it’s a small business building a showroom or a government constructing public infrastructure. Pre-engineered buildings are a cost-effective solution. How? They minimize material waste, optimize resource use, and require less on-site labor. The result is significant savings without compromising quality.
According to a report by Allied Market Research, the global PEB market is projected to grow at a CAGR of 13.9% from 2021 to 2030. In Nepal, where construction costs can escalate due to transportation and labor challenges, PEBs offer a budget-friendly alternative that doesn’t skimp on durability.
Construction Method | Cost per Sq. Ft. (Approx.) | Construction Time |
---|---|---|
Traditional Construction | 3375–5400 NPR | 6–12 months |
Pre-Engineered Buildings | 2025–3375 NPR | 2–6 months |
3. Built to Withstand Nepal’s Challenges
Nepal’s geography is as beautiful as it is challenging. From earthquakes to heavy rainfall, buildings here need to be tough. Pre-engineered buildings are designed with resilience in mind. Made from high-strength steel and engineered to precise specifications, PEBs can withstand seismic activity, extreme weather, and temperature fluctuations.
For instance, Nepal lies in a seismically active zone, with a history of devastating earthquakes like the one in 2015. PEBs’ lightweight yet sturdy designs make them less susceptible to structural damage, ensuring safety and longevity. This durability makes pre-engineered buildings the future for a country prone to natural disasters.
4. A Step Toward Sustainability
Sustainability is no longer a buzzword—it’s a necessity. Nepal’s construction industry is under pressure to adopt eco-friendly practices, and pre-engineered buildings deliver. By reducing construction waste and using recyclable materials like steel, PEBs align with global sustainability goals. Plus, their energy-efficient designs can lower long-term operational costs, a win for both the environment and your wallet.
For example, PEBs can incorporate insulation and energy-saving features, reducing the carbon footprint of buildings. In a country like Nepal, where environmental conservation is critical, pre-engineered buildings are paving the way for greener construction.
5. Unmatched Design Flexibility
One size doesn’t fit all, especially in Nepal’s diverse construction landscape. Whether you’re building a sleek showroom in Kathmandu, a sprawling warehouse in Biratnagar, or a modular home in Pokhara, pre-engineered buildings offer incredible design flexibility. Need to expand later? No problem—PEBs are modular, making additions or modifications a breeze.
This adaptability is a game-changer for Nepal’s growing economy, where businesses need spaces that evolve with their needs. From aesthetic facades to functional layouts, pre-engineered buildings provide endless possibilities.
Applications of Pre-Engineered Buildings in Nepal
The versatility of pre-engineered buildings makes them suitable for a wide range of projects. Here’s how they’re making waves across Nepal’s construction sector:
- Industrial Warehouses: Nepal’s industrial sector is growing, and PEBs provide affordable, durable storage solutions for factories and logistics hubs.
- Commercial Spaces: From retail showrooms to office complexes, PEBs offer modern designs that balance style and functionality.
- Residential Projects: Modular PEB homes are gaining traction for their affordability and quick construction, ideal for urban and rural areas alike.
- Agricultural Storage: Farmers need weather-resistant storage for crops and equipment. PEBs deliver cost-effective, long-lasting solutions.
- Community Infrastructure: Schools, health centers, and sports facilities benefit from PEBs’ quick assembly and durability.
Application | Key Benefit | Example Use Case |
---|---|---|
Industrial Warehouses | Cost-effective, scalable | Storage for manufacturing units |
Commercial Spaces | Aesthetic flexibility | Retail stores, office buildings |
Residential Projects | Quick assembly, affordability | Modular homes in urban areas |
Agricultural Storage | Weather resistance | Grain storage facilities |
Community Infrastructure | Durability, low maintenance | Schools, community centers |
The Numbers Behind the Trend
The global rise of pre-engineered buildings is undeniable. According to Grand View Research, the PEB market is expected to reach $28.9 billion by 2027, growing at a CAGR of 13.1%. In Nepal, this growth is mirrored by the increasing adoption of PEBs in industrial and commercial projects.
For instance, the number of PEB-based warehouses in Nepal’s industrial corridors, like those in Birgunj and Bhairahawa, has surged by 20% in the last five years, according to local industry estimates.
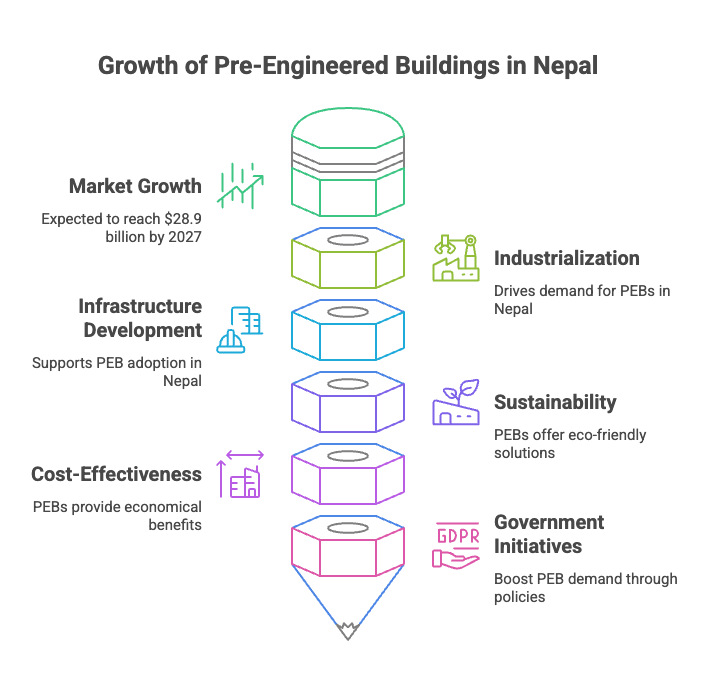
Why the surge? Nepal’s push for industrialization and infrastructure development, coupled with the need for sustainable and cost-effective solutions, makes pre-engineered buildings the future. Government initiatives to boost manufacturing and trade further amplify the demand for PEBs.
Why Choose a Local PEB Provider in Nepal?
Partnering with a trusted provider like PEB Nepal ensures that your project benefits from local expertise and global standards. Here’s what sets PEB Nepal apart:
- Tailor-Made Solutions: Customized designs to meet your specific needs, whether it’s a factory or a community center.
- Timely Delivery: Streamlined processes to ensure your project stays on schedule.
- Sustainability Focus: Eco-friendly materials and practices to align with Nepal’s environmental goals.
By choosing a local provider, you also support Nepal’s economy while ensuring your project adheres to regional building codes and seismic standards.
Overcoming Challenges with Pre-Engineered Buildings
While pre-engineered buildings offer numerous advantages, there are challenges to consider. For instance, some developers may be hesitant to adopt PEBs due to a lack of awareness or misconceptions about their durability. However, education and successful case studies are changing perceptions.
Additionally, Nepal’s rugged terrain can pose logistical challenges for transporting PEB components. Reputable providers mitigate this by optimizing logistics and partnering with reliable transport networks.
The Road Ahead for Pre-Engineered Buildings in Nepal
As Nepal continues to urbanize and industrialize, pre-engineered buildings will play a pivotal role in shaping its future. Their ability to deliver fast, affordable, and sustainable solutions makes them ideal for a country striving to balance growth with environmental responsibility.
Looking ahead, advancements in PEB technology—such as smart insulation, solar integration, and modular expansions—will further solidify their position as the future of construction. For businesses, developers, and communities in Nepal, embracing pre-engineered buildings is not just a smart choice—it’s a step toward a more resilient and sustainable tomorrow.
Conclusion
Pre-engineered buildings are not just a trend; they are the future of construction in Nepal. From cost savings and durability to sustainability and flexibility, PEBs offer a myriad of benefits that traditional methods cannot match. If you’re planning your next construction project, consider PEBs for a modern, efficient, and environmentally friendly solution.
Read More: Top 5 Benefits of PEB Structures for Industrial Projects in Nepal