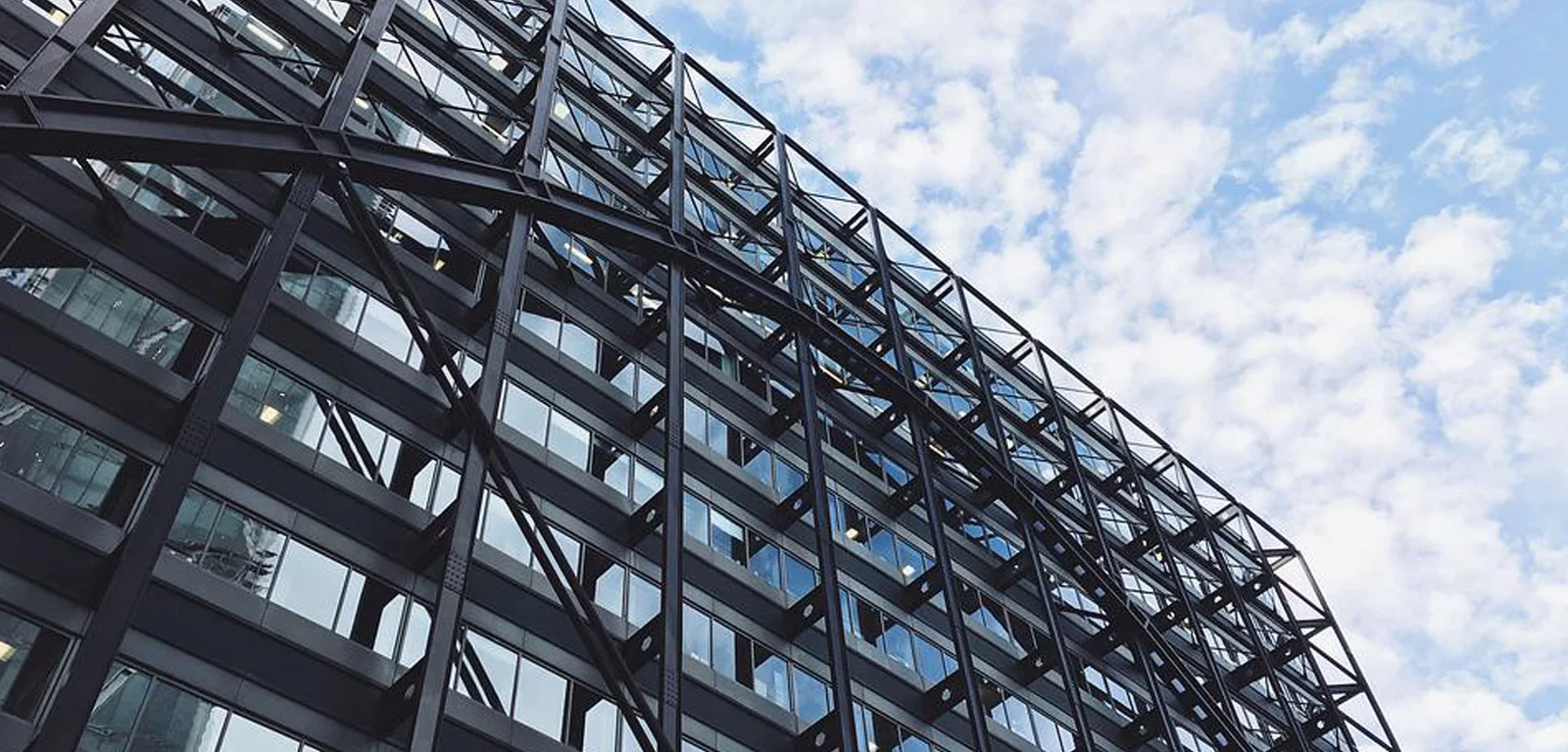
Pre-Engineered Buildings (PEBs) vs. Civil Construction: A Comprehensive Analysis
When choosing between PEBs vs. civil construction in Nepal, developers and homeowners must weigh cost, speed, and suitability to meet diverse project demands.
Nepal’s construction industry is at a crossroads, driven by rapid urbanization, industrial growth, and the need for resilient infrastructure. Developers, builders, and homeowners face a pivotal decision: opt for pre-engineered buildings (PEBs) or stick with traditional civil construction.
Both methods offer distinct advantages, but their differences in cost, time, durability, and suitability make them suited for specific needs in Nepal’s unique context.
This article provides an in-depth comparison of PEBs and civil construction, focusing on their application in Nepal. It includes detailed research, data, cost breakdowns, and practical insights to help you make an informed choice. With a focus on Nepal’s economic, geographic, and cultural landscape, we’ll explore how these methods align with modern demands.
Understanding Pre-Engineered Buildings (PEBs)
Pre-engineered buildings are steel structures designed and manufactured in factories before being transported to the construction site for assembly. These buildings rely on standardized components, such as steel frames, columns, beams, and cladding, which are bolted together on-site.
PEBs are widely used for industrial and commercial projects like warehouses, factories, poultry sheds, and retail spaces. In Nepal, PEBs are gaining traction due to their efficiency, affordability, and adaptability to diverse terrains.
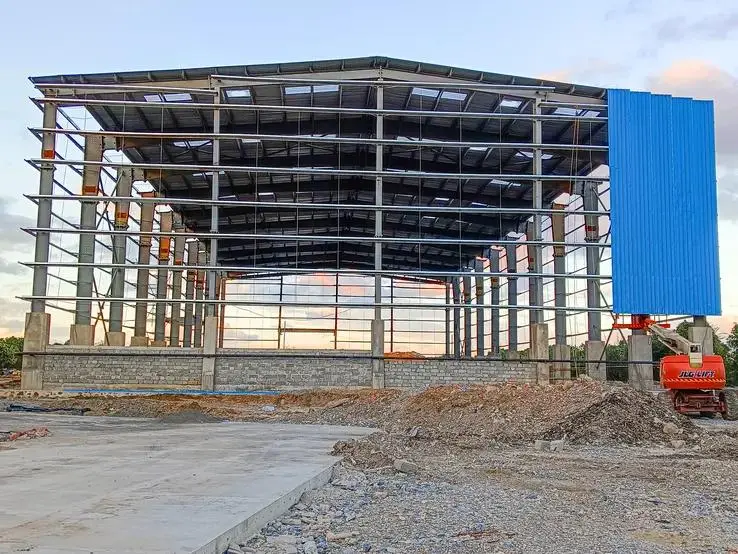
The design process for PEBs involves advanced software that optimizes material use, reducing waste. Factories produce components to exact specifications, ensuring precision.
On-site assembly is quick, as workers simply connect pre-fabricated parts. This method minimizes reliance on skilled labor and heavy machinery, making it ideal for Nepal’s challenging construction environment.
Understanding Civil Construction
Civil construction, often called conventional or traditional construction, involves building structures on-site using materials like concrete, bricks, cement, and timber. This method relies heavily on manual labor, on-site material preparation, and customized designs.
In Nepal, civil construction dominates residential projects, schools, hospitals, and cultural buildings. It allows architects to create tailored designs that reflect local aesthetics and functional needs.
Civil construction starts with laying foundations, followed by erecting walls, casting concrete slabs, and finishing interiors. Each step requires skilled masons, carpenters, and laborers. While versatile, this method is time-intensive and susceptible to delays from weather, material shortages, or labor issues.
Detailed Comparison: PEBs vs Civil Construction
To choose the right method, understanding their differences is crucial. Let’s examine key factors: construction time, cost, durability, flexibility, and environmental impact.
1. Construction Time
Time is a critical factor in Nepal, where project delays can disrupt budgets and operations.
- PEBs: PEBs significantly reduce construction timelines. Since components are pre-fabricated in controlled factory settings, on-site work focuses on assembly. For instance, a 10,000 sq. ft. PEB warehouse in Nepal can be completed in 5–6 months, including site preparation and assembly. This speed is a game-changer for businesses needing quick setups, such as factories or storage facilities in Kathmandu or Biratnagar.
- Civil Construction: Conventional construction is slower. A similar 10,000 sq. ft. structure, like a commercial building, may take 12–24 months. Tasks like foundation pouring, bricklaying, and concrete curing are time-consuming. Monsoon seasons in Nepal, which last from June to September, often halt progress, extending timelines further.
2. Cost Efficiency
Cost is a top concern in Nepal, where budgets are often constrained.
- PEBs: PEBs are cost-effective due to their efficient use of materials and labor. Standardized designs reduce engineering expenses, and pre-fabrication minimizes waste. In Nepal, PEBs cost NPR 2,000–4,000 per sq. ft., depending on design complexity and location. For a 10,000 sq. ft. warehouse, total costs range from NPR 20–40 million, covering steel structures, cladding, and basic finishes.
- Civil Construction: Civil construction is pricier due to higher material and labor demands. Costs for a basic residential house start at NPR 3,000–3,500 per sq. ft., while mid-range homes cost NPR 4,000–5,500 per sq. ft. Premium projects, like luxury homes in Kathmandu, exceed NPR 6,000 per sq. ft. A 1,000 sq. ft. single-storey house costs NPR 30–55 million, including materials, labor, and finishes. Material waste and fluctuating prices for cement and bricks further inflate costs.
3. Durability and Maintenance
Nepal’s seismic activity and harsh weather demand durable structures.
- PEBs: PEBs use high-grade steel with protective coatings, such as galvanized or powder-coated finishes, to resist corrosion and weathering. These buildings are lightweight yet strong, making them ideal for earthquake-prone regions like Nepal. Maintenance is minimal, with occasional checks for rust or bolt tightening. Over 20–30 years, PEBs incur low upkeep costs.
- Civil Construction: Concrete and brick structures are durable but susceptible to cracks, especially in seismic zones. Poor construction practices, common in Nepal, can exacerbate this issue. Maintenance involves regular repairs for cracks, leaks, and plaster damage, increasing long-term costs. Reinforced concrete buildings, when built to code, withstand earthquakes but require costly retrofitting if standards are not met.
4. Design Flexibility
Customization is vital for residential and cultural projects in Nepal.
- PEBs: PEBs offer flexibility within modular constraints. They excel in creating large clear spans (up to 90 meters) without internal columns, ideal for warehouses and factories. However, their box-like designs may not appeal to homeowners seeking traditional aesthetics. Recent advancements allow for some customization, like adding facades or insulation, but options are limited compared to civil construction.
- Civil Construction: This method shines in customization. Architects can design intricate homes, temples, or offices that reflect Nepal’s cultural heritage, such as Newari or Tharu styles. Homeowners can choose layouts, finishes, and materials to suit personal tastes. However, custom designs increase costs and require skilled labor, which can be scarce in rural Nepal.
5. Environmental Impact
Sustainability is gaining attention in Nepal’s construction sector.
- PEBs: PEBs are eco-friendly. Steel is recyclable, and pre-fabrication reduces waste by 10–20% compared to civil construction. Insulated panels improve energy efficiency, cutting cooling and heating costs by 15–25%. In Nepal, where energy costs are rising, this is a significant advantage.
- Civil Construction: Conventional methods produce more waste, including excess concrete, broken bricks, and packaging. On-site mixing and cutting generate debris, impacting the environment. Energy-intensive processes, like cement production, contribute to carbon emissions. However, using local materials like mud or bamboo can reduce the environmental footprint in rural areas.
Read More: Eco-Revolution: PEB Environmental Impact for a Sustainable Future
PEBs vs Civil Construction: Cost Breakdown in Nepal (2025)
Let’s dive into the financial details, as costs heavily influence decisions in Nepal.
PEB Costs
PEB pricing depends on factors like size, steel quality, and site conditions. In Nepal, costs range from NPR 2,000–4,000 per sq. ft. This includes steel frames, roofing, cladding, and basic insulation. For a 10,000 sq. ft. industrial shed, total costs are NPR 20–40 million. Additional expenses, like foundation work or interior finishes, may add NPR 5–10 million, depending on specifications.
Civil Construction Costs
Civil construction costs vary by project type and location. Urban areas like Kathmandu and Pokhara are pricier due to higher labor and material costs. A basic 1,000 sq. ft. house costs NPR 30–35 million, while mid-range homes range from NPR 40–55 million. Premium constructions, with imported finishes, can exceed NPR 60 million. Commercial buildings, like offices, cost NPR 30–60 million for 10,000 sq. ft., driven by material and labor expenses.
Cost Comparison Table
Aspect | PEB (NPR) | Civil Construction (NPR) |
---|---|---|
Cost per sq. ft. | 2,000–4,000 | 3,000–6,000+ |
10,000 sq. ft. Warehouse | 20–40 million | 30–60 million |
1,000 sq. ft. House | Not applicable | 30–55 million |
Construction Time | 5–6 months | 12–24 months |
Maintenance Costs | Low (NPR 50,000/year) | High (NPR 200,000/year) |
Material Waste | Minimal (5–10%) | High (20–30%) |
Note: Costs exclude permits, taxes, and advanced finishes. Prices vary by region and material quality.
Material Costs in Nepal (2025)
Material prices directly impact budgets. Here’s a detailed breakdown based on market trends:
Material | Price (NPR) | Used In |
---|---|---|
Cement (50 kg bag) | 800–1,200 | Civil Construction |
TMT Steel Bars (per kg) | 100–120 | Both (more in PEBs) |
Bricks (per unit) | 15–20 | Civil Construction |
Sand (per cubic ft.) | 50–80 | Civil Construction |
PEB Steel Structure | 2,000–4,000/sq. ft. | PEBs |
Ready-Mix Concrete | 12,000–15,000/cu. m. | Civil Construction |
Steel prices have risen 15% since 2023, impacting PEB costs. Cement prices increased by 27% in 2025, affecting civil construction budgets.
Advantages of PEBs in Nepal
PEBs are reshaping Nepal’s construction landscape. Their benefits include:
- Rapid Construction: PEBs cut project timelines by up to 50%, critical for businesses needing quick occupancy.
- Cost Savings: Lower material and labor costs save 20–30% compared to civil construction.
- Seismic Resistance: Lightweight steel frames flex during earthquakes, reducing collapse risks in Nepal’s seismic zones.
- Sustainability: Recyclable steel and minimal waste align with Nepal’s green building initiatives.
- Scalability: Adding bays or sections for future expansion is straightforward and cost-effective.
Read More: Top 5 Benefits of PEB Structures for Industrial Projects in Nepal
Advantages of Civil Construction in Nepal
Civil construction remains the backbone of Nepal’s residential and cultural projects. Its strengths include:
- Cultural Alignment: Brick and concrete designs reflect Nepal’s traditional architecture, like Newari courtyards or Tharu mud houses.
- Customization: Homeowners can tailor layouts, finishes, and aesthetics to personal or regional preferences.
- Local Materials: Abundant sand, bricks, and cement reduce reliance on imports.
- Longevity: Well-built concrete structures last 50+ years with proper maintenance.
- Community Labor: Civil construction supports local economies by employing unskilled and skilled workers.
Challenges of PEBs vs Civil Construction
Both methods face hurdles in Nepal’s context.
PEB Challenges
- Aesthetic Limitations: PEBs’ modular designs may not appeal to homeowners seeking traditional looks.
- Skilled Labor Shortage: Nepal has limited workers trained in PEB assembly, increasing reliance on specialized contractors.
- Steel Price Fluctuations: Global steel price volatility can raise costs unexpectedly.
- Transport Logistics: Delivering pre-fabricated components to remote areas like Mustang or Solukhumbu is costly.
Civil Construction Challenges
- Weather Delays: Monsoons and harsh winters halt construction, especially in hilly regions.
- Cost Overruns: Rising cement and labor costs lead to budget overruns, with 30% of projects exceeding estimates.
- Quality Control: Inconsistent construction practices in rural Nepal result in substandard buildings.
- Environmental Impact: High waste and energy use clash with sustainable building goals.
Suitability in Nepal’s Context: PEBs vs Civil Construction
Nepal’s geography, economy, and seismic risks shape construction choices.
- PEBs: Ideal for industrial and commercial projects in urban hubs like Kathmandu, Pokhara, and Biratnagar. Their speed and earthquake resistance suit factories, warehouses, and retail spaces. PEBs are less common in residential projects due to aesthetic preferences.
- Civil Construction: Preferred for homes, schools, and cultural buildings. Nepal’s cultural emphasis on traditional designs makes civil construction dominant in residential areas. In rural regions, local materials like mud and bamboo keep costs low.
Nepal lies in a high seismic zone, with a history of devastating earthquakes (e.g., the 2015 Gorkha earthquake). PEBs’ lightweight steel frames absorb seismic forces better than rigid concrete structures. However, civil constructions, when reinforced with modern techniques, also meet seismic standards.
Market Trends in Nepal
The PEB market in Nepal is growing at 25–30% annually, driven by demand for industrial and commercial spaces. The rise of e-commerce and manufacturing fuels this trend. Civil construction remains dominant, with 70% of residential projects using this method. However, cement price hikes (27% in 2025) and labor shortages are pushing developers toward PEBs for cost-sensitive projects.
Decision Factors: PEBs vs Civil Construction
Your choice depends on project goals, budget, and location.
- Choose PEBs for:
- Industrial or commercial projects needing quick completion.
- Budget-conscious developments in urban or semi-urban areas.
- Earthquake-prone regions requiring lightweight, flexible structures.
- Sustainable projects with low maintenance needs.
- Choose Civil Construction for:
- Residential homes or cultural buildings requiring unique designs.
- Projects prioritizing traditional aesthetics, like Newari or Buddhist styles.
- Rural areas with access to local materials and labor.
- Long-term investments where customization outweighs time concerns.
Future Outlook
Nepal’s construction sector is poised for transformation. PEBs will likely dominate industrial and commercial projects due to their efficiency and sustainability. Advances in PEB technology, like 3D modeling and modular insulation, will enhance their appeal.
Civil construction will remain relevant for residential and heritage projects but must adopt greener practices to stay competitive. Government initiatives, like the National Earthquake Reconstruction Program, emphasize seismic-resistant designs, benefiting both methods.
Conclusion
Pre-engineered buildings and civil construction serve distinct purposes in Nepal. PEBs excel in speed, cost savings, and seismic resistance, making them ideal for industrial and commercial needs. Civil construction offers unmatched customization and cultural alignment, perfect for homes and heritage projects. Costs for PEBs range from NPR 20–40 million for a 10,000 sq. ft. warehouse, while civil construction costs NPR 30–55 million for a 1,000 sq. ft. house.
Evaluate your project’s scope, budget, timeline, and aesthetic needs to choose the right method. Consult with local engineers and contractors to ensure compliance with Nepal’s seismic and environmental standards. Both approaches, when executed well, can deliver durable, functional structures for Nepal’s growing infrastructure demands.
Read More: Ultimate Checklist for Choosing the Right PEB Company in Nepal