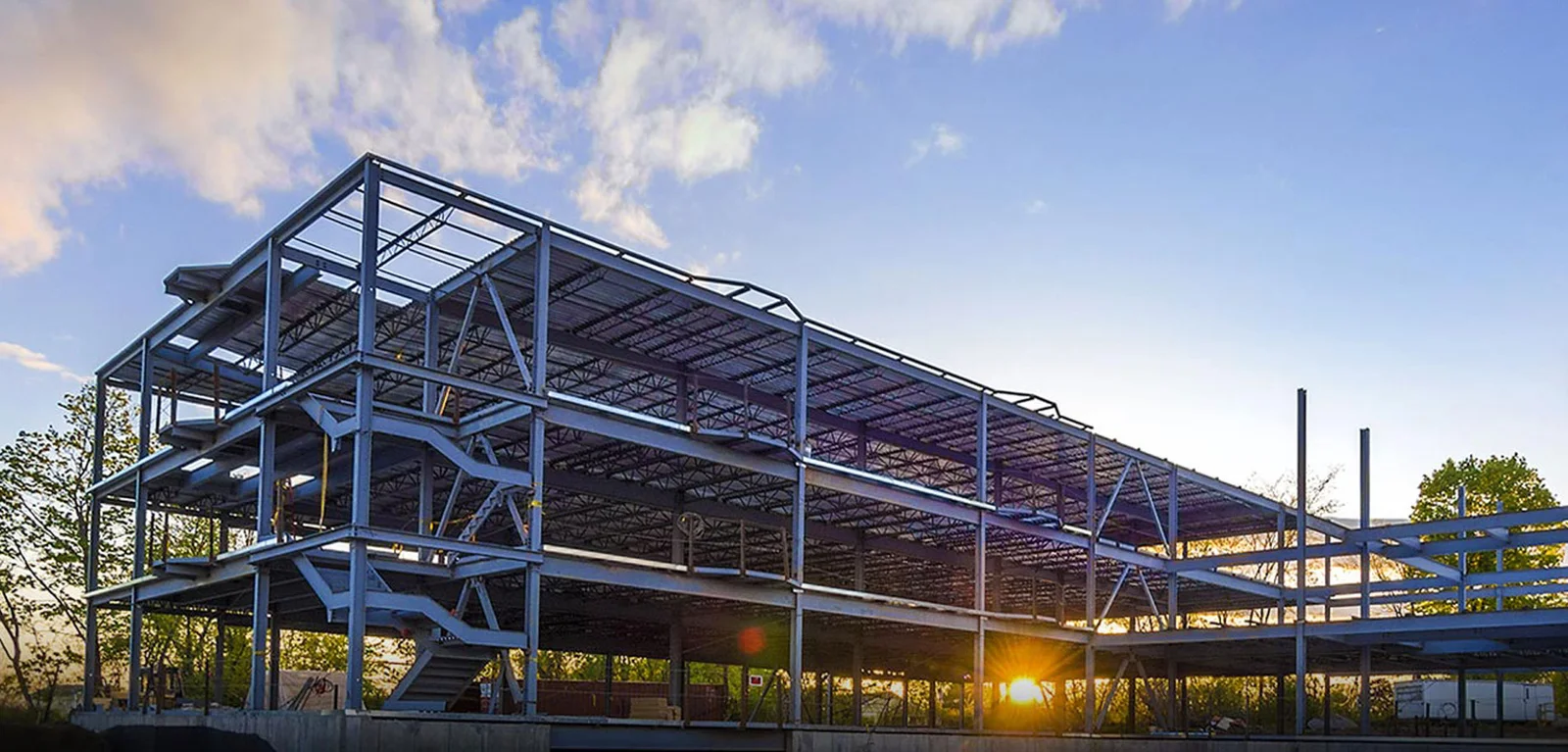
PEB Cost Nepal: How Pre-Engineered Buildings Save Money in Construction
In Nepal’s rapidly growing construction sector, the cost of PEB (Pre-Engineered Buildings) is revolutionizing how developers balance affordability, quality, and sustainability. PEBs offer a cost-efficient alternative to traditional methods, delivering faster construction, reduced material waste, and long-term savings. This article explores how PEBs are transforming Nepal’s construction landscape with their economic and eco-friendly advantages.
This article explores how PEB save money, their cost components, and their role in promoting sustainable construction in Nepal.
Time is Money: Faster Construction with PEBs
PEBs significantly reduce construction timelines, directly impacting project budgets.
- Factory Fabrication: PEB components are pre-manufactured in controlled factory environments, cutting on-site construction time by up to 50% compared to traditional methods.
- Cost Impact: Shorter timelines reduce labor costs, equipment rental fees, and project management expenses. For example, a traditional warehouse might take 6–8 months to build, while a PEB structure can be completed in 3–4 months.
- Challenges with Traditional Methods: Weather delays, material shortages, and manual labor inefficiencies often inflate costs in conventional construction.
Construction Type | Timeline (Months) | Est. Labor Cost (NPR/sq.m) | Total Cost Savings |
PEB | 3-4 | 2500-3500 | 30%-50% less |
Traditional | 6-8 | 4000-5500 | – |
Note: Costs are hypothetical estimates based on industry standards for a medium-sized warehouse (1,000 sq.m) in Nepal, 2025.
Cost-Effective Materials and Minimal Wastage
Material waste is a significant cost driver in traditional construction, but PEBs optimize resource use.
- Precise Engineering: PEB components are designed with precision, minimizing excess material during fabrication and installation.
- Recyclable Steel: Steel, the primary PEB material, is 100% recyclable, reducing disposal costs and aligning with sustainable construction goals.
- Cost Breakdown: Material costs for PEBs are typically 20–30% lower than traditional methods due to reduced waste and efficient design.
Material Type | PEB Cost (NPR/Sq.m) | Traditional Cost (NPR/sq.m) | Waste Percentage |
Steel (PEB) | 3000-4000 | – | 2-5% |
Concrete/Brick | – | 5000-7000 | 10-15% |
Note: Costs are indicative and vary based on project size and location.
Lower Maintenance and Energy Costs
Building maintenance is an often-overlooked expense, but PEB structures excel in reducing long-term costs.
- Energy Efficiency: PEBs incorporate insulated panels, reflective roofing, and optimized ventilation, reducing energy consumption for heating and cooling by 20–30%.
- Durability: Corrosion-resistant steel ensures PEBs require minimal maintenance, unlike traditional buildings that face frequent repairs due to weathering.
- Cost Savings: Annual maintenance costs for PEBs can be 50% lower than for traditional structures, and energy savings further reduce operational expenses.
Building Type | Maintenance Cost (NPR/sq.m/year) | Energy Cost (NPR/sq.m/Year) | Total Annual Savings |
PEB | 100-150 | 200-300 | 40-50% |
Traditional | 200-300 | 400-600 | – |
Note: Estimates assume a commercial building with standard HVAC systems.
This makes PEBs a cheaper and safer option for both commercial and industrial projects.
Earthquake-Resistant and Sustainable Design
Nepal’s seismic activity makes earthquake-proof construction essential.
- Seismic Resilience: PEBs are engineered with flexible steel frames that absorb seismic shocks, reducing the risk of structural damage.
- Cost Implications: Earthquake-resistant designs lower repair costs post-seismic events, with PEBs potentially saving 60–80% on reconstruction compared to damaged traditional buildings.
- Sustainability: PEBs align with UN Sustainable Development Goals by promoting resilient infrastructure, making them a safer and greener choice.
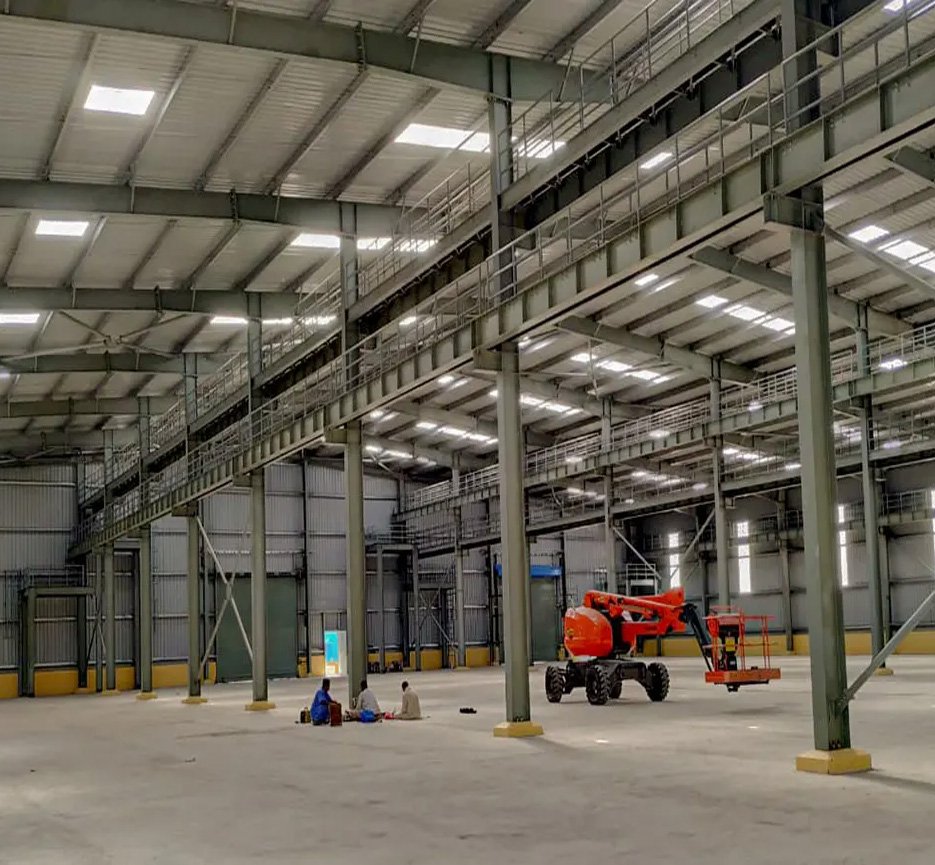
Investing in PEBs is a proactive approach to minimizing risks and maximizing returns.
Customization and Scalability Save Money
Traditional buildings often require significant modifications to adapt to future needs, adding to costs.
- Modular Design: PEBs can be easily expanded or reconfigured, with additional components integrated at 30–40% lower cost than traditional renovations.
- Cost Efficiency: Scalable designs minimize expenses for businesses needing to adapt spaces for growth or new purposes.
- Example: Adding a 200 sq.m extension to a PEB structure might cost NPR 800,000–1,200,000, compared to NPR 1,500,000–2,000,000 for traditional construction.
This adaptability ensures long-term savings for growing businesses.
Cost Breakdown of PEB Construction in Nepal
To provide clarity, here’s a hypothetical cost breakdown for a 1,000 sq.m PEB warehouse in Nepal (2025).
Component | Cost (NPR/sq.m) | Total Cost (NPR, 1000 Sq.m) |
Materials (Steels, Panels) | 3500-4500 | 3,500,000–4,500,000 |
Fabrication | 1000-1500 | 1,000,000–1,500,000 |
Installation/Labor | 2500-3500 | 2,500,000–3,500,000 |
Foundation | 1500-2000 | 1,500,000–2,000,000 |
Total | 8500-11500 | 8,500,000–11,500,000 |
Note: Costs exclude land, permits, and taxes. Traditional construction for a similar structure may cost NPR 12,000–15,000/sq.m.
Conclusion
Pre-Engineered Buildings are transforming Nepal’s construction landscape by offering cost-efficient, eco-friendly, and sustainable solutions. With faster construction, reduced material waste, lower maintenance costs, seismic resilience, and scalable designs, PEBs deliver significant savings without compromising quality. For businesses and developers in Nepal, adopting PEBs is a smart investment in both financial and environmental sustainability.
Ready to explore PEBs for your next project? Contact PEB Nepal for expert guidance on cost-effective, sustainable construction solutions.
Read More: Ultimate Checklist for choosing RIght PEB Company in Nepal